QUALITY CONTROL
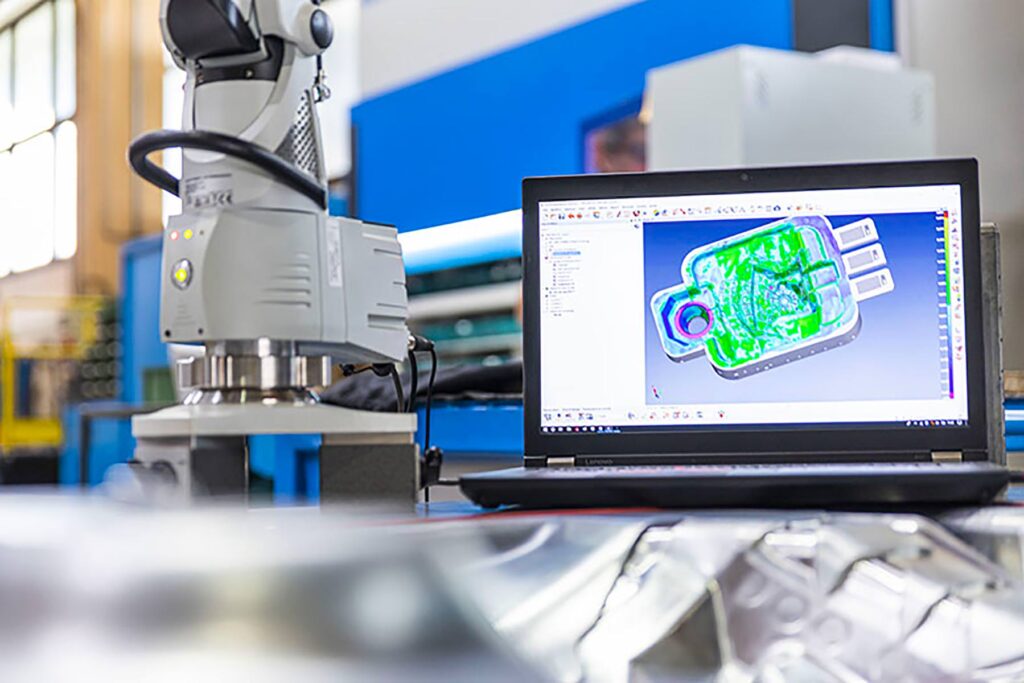
All molds delivered to the Customer must first pass the testing stage of our Quality Control department. This way we know we are delivering a perfect mold to the Customer, ready to be entered into the production cycle.
- Final verification of the mold design and first sampling
The mold made is functionally tested and checked in every component, and finally an initial sampling is made with the testing of the mold.
- Mold dimensional scanning
In order to ensure increasingly precise quality controls, we have integrated the “Absolute Arm 7525” into our instrumentation fleet. A state-of-the-art instrument that allows us to perform dimensional checks on the molding parts and to photograph the workpiece in real time, while comparing it with the mathematics developed by design. In this way, we are always in control of the precision level of the machine tools and the efficiency of the production process, so that we can effectively intervene to optimize the job flow and achieve a flawless result within the required delivery time.
- Checking the tightness of cylinders
When the mold is fully assembled, we perform leak testing of the hydraulic cylinders, tested up to a pressure of about 260 Bar.
- Thermoregulation circuit control
We perform cold and hot checks of the temperature control circuits of the various mold parts up to a temperature of about 100°. The cooling circuits are an essential part of the perfect operation of the molding process, so this testing phase is essential before delivery to the Customer.
- Delivery to customer for approval and validation
The mold tested by the quality control department is sent to the Customer together with all agreed samples and control documents.
In case it is necessary, a mold tune-up is first carried out for any nonconformities or improvements in functionality.
Contact us
Fill out the form to be contacted by one of our consultants as soon as possible.